As discussed in the previous post, plane blades from the 19th century were typically made of a wrought iron backing with a hard steel bit welded to the tip[1].
To better understand the history of these and other edge tools created in this era we can take a look at the processes used to create the raw materials. We'll focus on what was happening around 1850, the zenith of hand tool manufacturing in Great Britain.
Pig Iron
There are iron rich ores found all over the world and the starting point to steel production is to refine this crude material. A blast furnace is used to melt the iron ore and – once the slag (oxidized impurities from the ore) has been skimmed off – the resulting molten metal is poured into moulds.
The ores contain varying amounts of silica and other impurities and, although fluxes were added to remove these unwanted chemicals during the refining process, the process was imperfect and remaining adulterants would interfere with subsequent processing. Particularly problematic are sulphur and phosphorus, the presence of which change the behaviour of steel when it is heat treated (see the discussion on “hot-short” steel here), so sources of clean iron ore were highly sought after.
The molten iron was poured into moulds made in a sand bed and arranged with a large central trough and many smaller troughs running from it at right angles. These moulds – redolent of a pig suckling its young – give the iron its name.
Pig-iron was of limited use since the amount of carbon introduced to the metal from the burning fuel made it very brittle.
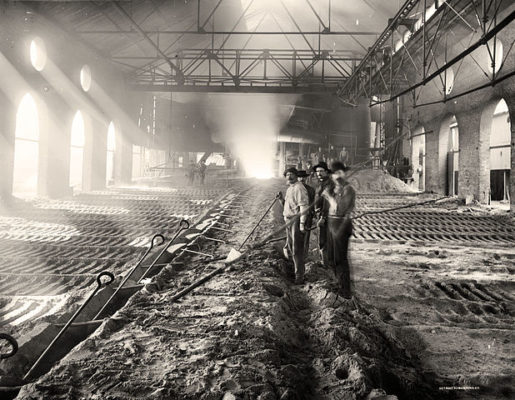
Refined Pig-Iron
Steel is made from iron combined with around 1% carbon. The presence of the appropriate amount of carbon creates a metal that can be forged and hardened.
Over centuries of experimentation it was learned that a reliable way to create steel was to begin by removing the carbon from pig-iron (which contained variable quantities of carbon but generally too much for making steel) and then to add back a small amounts of carbon using techniques that allowed this to be done in a controlled and repeatable fashion.
Two important technologies for removing carbon and other impurities from pig-iron were invented: the puddling process, which relied on coal fired furnaces, and the Lancashire process which used charcoal. The former was the primary technique used in Sheffield where charcoal had become scarce during the industrial revolution but coal was available in large quantities.
Sweden – the primary supplier of refined iron for Sheffield tool makers – relied on the Lancashire process since they had a plentiful supply of trees but no local coal.
Wrought Iron – the Puddling Process
The process for puddling iron as practised at the Lightmore Works in Shropshire was described by a visitor in the 1820s as follows:
The different stages of the manufacture from the ore to the making blooms are briefly the following:
1. The roasted ore being mixed with limestone is reduced in the high smelting furnaces with coke which are tapped at regular intervals and the melted iron runs into furrows made in sand and thus forms pigs
2. The pigs being broken into two or three pieces each are re melted in the refinery furnace with coke and the produce being let out into a shallow flat cast iron trough forms thick plates called slabs
3. The slabs being broken are melted in the puddling furnace with coal and brought out in large masses called balls which while yet glowing hot are…
4. Laid under a very heavy hammer and stamped into plates which are then thrown into water in order to cool them
5. The plates being broken the pieces are piled one on the other to the height of about a foot and a half and placed in a reverberatory furnace called a balling furnace[2] from which when sufficiently heated by coal they are removed to the shingling hammer where they are beaten into short thick bars called blooms.
The Franklin Journal and American Mechanics Magazine, 1826
A puddling furnace is a type of a reverberatory furnace. This means that the burning fuel on the grate is isolated from the hearth to reduce the chance of impurities from the fuel being mixed with the metal:
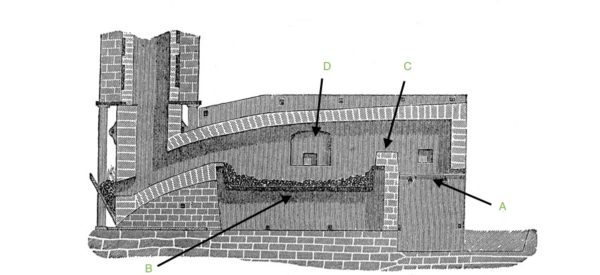
Coal is added through the small hole above the grate (A). A sliding door is suspended in front of a doorway (D) by a chain attached to a lever above the workman’s head and is raised for the charge and discharge of iron:
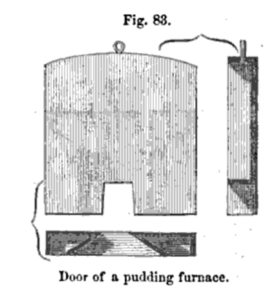
The small hole at the bottom of this door is designed to allow the puddler to use his tools without being exposed to full heat of the furnace.
First of all the shallow bowl shaped hearth was sealed with a mixture of slag and cinders to prevent the heat melting the iron plates underneath. After the hearth was prepared the fires were stoked on the grate until the furnace reached the correct temperature.
Once the furnace was sufficient hot, broken up pig-iron bars were fed into the hearth and, once melted, the puddler used long iron bars called ‘rabbles’ pushed through the hole in the working door to continuously stir the molten metal, maximising the contact with the air and heat so that the carbon contained in the metal oxidised and burned off.
One of the side-effects of the high levels of carbon present in the pig iron was to reduce its melting point and consequently, as the metal was decarbonised, the melting point rose also causing the metal to solidify. The puddler relied on this fact to determine when the process was complete: when the metal eventually solidified in the hearth it was said to have ‘come to nature’ and could be extracted from the furnace for further processing.
As the liquid metal began to come to nature it formed small round particles which grew larger under the manipulation of the puddler who would work them by breaking up and turning the lumps of metal until several round balls (sometimes referred to as loops or loups) of about 12-15 inches in diameter were formed[3].
Once the balls are complete the helper lifts the door and the balls are removed. The job of the puddler was renowned for being highly skilled and physically demanding – each ball typically weighed 70-80lbs and was white hot. The example in the photograph below weighed around 120lbs!
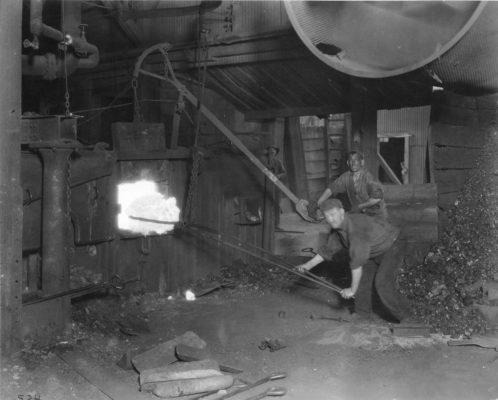
The iron at this stage would contain areas of slag and cinder that were introduced as the metal was stirred. To make the metal more uniform it was worked ("wrought") with hammers in a process called shingling and this caused some of the of the slag to be expelled from the metal and for the small amounts that remained to be stretched into elongated filaments that give the metal a distinctive grain structure. The working of the metal with a hammer is the source of the term wrought iron.
Finally the hot metal is pushed through rollers to create long bars and thus the final product was often referred to simply as ‘bar iron’.
The small amounts of slag and low carbon content of wrought iron gives it some useful properties including weldability, toughness and rust resistance. The metal was sometimes referred to as ‘malleable iron’ in virtue of its toughness, however, this term – like so many others in the iron and steel industry – was not always used consistently and the usage changed over time.
The puddling process required skilled labour and expensive machinery to produce any significant volume of wrought iron, and the process could not be scaled up easily since the amount processed was limited by the quantity of metal that could be manipulated by the puddler.
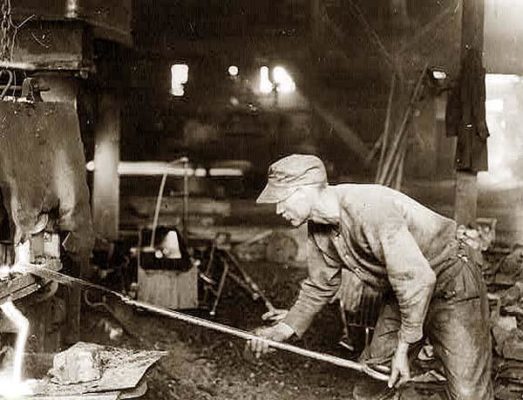
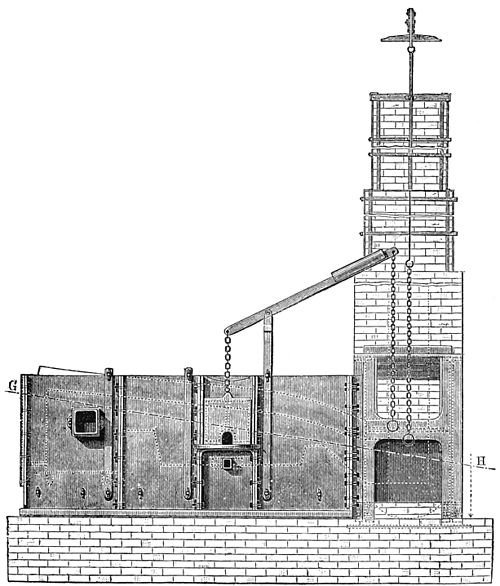
Eventually the puddling process was superseded by more efficient techniques created by Bessemer and Siemens, but the unique properties granted to puddled wrought-iron through the presence of filaments of slag were not retained in the low-carbon iron produced by the new processes.
Wrought iron is no longer made, but a working puddling furnace at Blists Hill, Shropshire, has been reconstructed using equipment salvaged from Thomas Walmsley’s Atlas works in Bolton. Wrought iron was produced at the Atlas works until the 1970s, making it the last commercial puddling furnace in the UK .
Attempts to make wrought iron using the reconstructed furnace have thus far been unsuccessful, but the machinery is still used to recycle salvaged wrought iron.
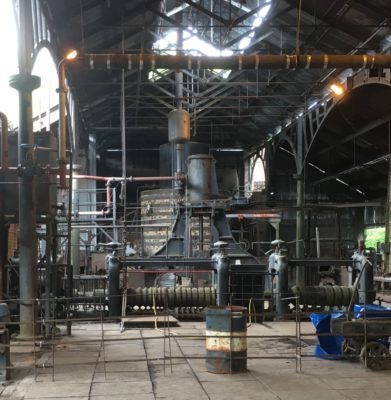
You can see the balling furnace, hammer and rollers in use in this video:
Swedish Wrought Iron – The Lancashire Hearth Process
As the name suggests, this method of refining pig iron was introduced to Sweden based on forges the inventor (Gustav Ekman) saw while visiting Lancashire, England, in the 1830s.
The furnace consisted of a a tall chimney at one end of the hearth and an gas convertor at the other.
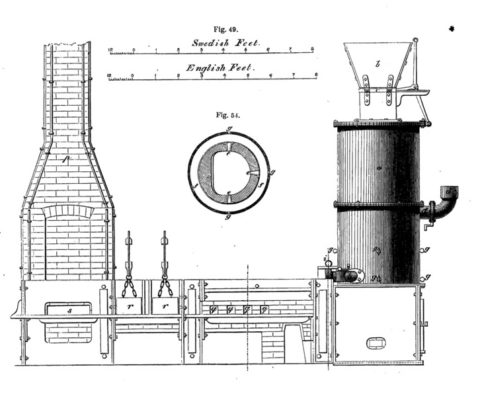
Ekman's 1843 invention made it possible to create gas from charcoal that burned at a higher temperature than the charcoal, allowing the furnace to get hot enough to act as a puddling furnace. The gas convertor (shown on the right in the diagram above) could supply gas to multiple furnaces. Pig iron was added through a door in the front of the furnace and the gas from the charcoal burned in the gas generator was blasted through nozzles on the side of the furnace into the fireplace where it ignited and heated the bottom of the cast-iron hearth. As with the puddling process the molten metal had to be stirred and then worked with hammers once it had ‘come to nature’ and the solid mass of iron was finally rolled into long bars.
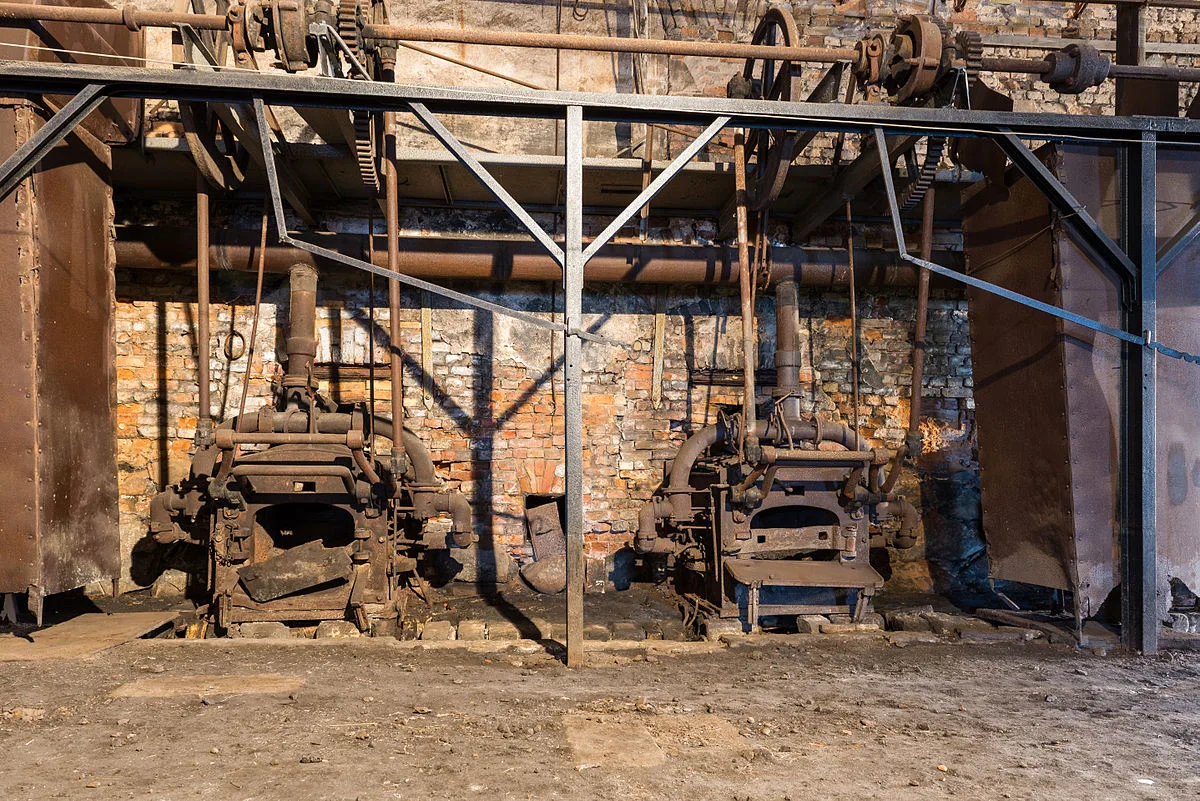
The high quality iron ore that was available in certain parts of Sweden and the relatively clean fuel used in the Lancashire Hearth process meant that the resulting bar iron was of consistently high purity and consequently Sheffield tool makers would demand Swedish iron even though locally produced puddled iron was significantly cheaper[4].
that’s it for iron – next topic blister steel
References
1⏎ | towards the end of the end of the century solid steel plane cutters and chisels became increasingly popular and the discovery of new steel making processes meant it was cheaper to use mild steel for the backing of laminated edge tools, but we will come on to that later |
2⏎ | A balling furnace was the general term used at the time to refer to the furnace where blooms of puddled iron were heated and welded together prior to rolling into bars. |
3⏎ | the Manufacture of Iron in all its Various Branches p268 |
4⏎ | there is a good overview of the state of the iron and steel industry – including the an explanation of some of the processes described above and confirmation of the preference for Swedish iron – in this paper produced by Charles Sanderson, a Sheffield steel maker, in 1855: On the Manufacture of Steel, as carried on in this and other Countries |